
TFT LCD ekranın yapısı
Sıvı Kristal Panel (Panel): Bu, görüntünün sunulmasından sorumlu olan ekranın ana parçasıdır. Sıvı kristal panel, aralarında sıvı kristal hücresi olarak bilinen bir sıvı kristal tabakası bulunan iki cam plakadan oluşur.
Polarize filtreler:Bu bileşenler sıvı kristal hücresinin her iki tarafında yer alır ve hücreden geçen ışığı işlemekle görevlidir.
Renk Filtresi: Genellikle kapalı sıvı kristal hücresinin cam plakalarından birinin üzerine işlenerek renkli görüntüleme amacıyla kullanılır.
İnce Film Transistör Dizisi (TFT Dizisi):Sızdırmaz sıvı kristal hücresinin diğer cam plakasına konumlandırılarak, ekranın çalıştırılmasında aktif rol oynar.
Arka aydınlatma:TFT-LCD ekran modülünün arkasında bulunan ışık kaynağı, sıvı kristal hücresi aracılığıyla görülebilen görüntünün üretilmesi için gerekli ışığı sağlar.
Harici Sürücü Devresi:Bu devreler, TFT dizisini ve arka aydınlatmayı uygun şekilde çalıştırmak için giriş görüntü sinyallerini yönetmekten sorumludur.

TFT LCD ekranların üretim süreci
Film Oluşumu:Sputtering (SPT) ve Kimyasal Buhar Biriktirme (CVD) gibi teknikler, alt tabaka üzerine birden fazla katman biriktirir.
Fotolitografi: Fotorezistin uygulanması, açığa çıkarılması ve geliştirilmesiyle mikro yapılar oluşturulması.
Aşındırma: Islak ve kuru aşındırma yöntemleri, belirli alanları kaldırarak alt tabakayı şekillendirir.
Soyunma: Desenleme sonrası, alt tabakayı temizlemek için fazla malzemeler çıkarılır.
Yardımcı işlem adımları:
Temizlik:Alt tabakanın kontaminasyondan arındırılmasını sağlar.
İşaretleme ve Pozlama:Alt tabaka kenarlarını belirler ve hazırlar.
Otomatik Optik Muayene (AOI):Arıza muayenesinde kullanılır.
Mikroskobik İnceleme ve Makroskobik İnceleme (Mic/Mac):Detaylı kontrol.
Film Performans Testi:Levha direnç ölçerler, profilometreler, reflektometreler/elipsometri, Fourier dönüşümlü kızılötesi spektroskopisi gibi araçları kullanır.
Açık/Kısa (O/S) Elektriksel Test:Devre sürekliliğini ve kısa devreleri kontrol eder. Test Elemanı Grubu (TEG) Elektriksel Test: Elemanların elektriksel performansını test eder.
Dizi Elektriksel Test:Dizinin elektriksel işlevselliğini sağlar.
Lazer Onarımı:Muayene sonuçlarına göre herhangi bir kusuru düzeltir.
Fotorezist Yeniden İşleme (PR Yeniden İşleme):Gerektiğinde fotolitografi adımlarını ayarlar veya tekrarlar.
Film Yeniden İşleme: Gerektiğinde film oluşum sürecini değiştirir veya mükemmelleştirir.

OC Katmanı Renk filtre desenlerini korur ve hazırlar.
RGB Katmanı Kaplama, pozlama ve geliştirme dizileri yoluyla oluşum.
BM (Siyah Matris) Katmanı Kontrastı artırır ve ışık sızıntısını sınırlar.
PS (Fotoğraf Aralayıcı) Katmanı Görüntü kalitesi için kritik öneme sahip olan alt tabakalar arasında hassas boşluk sağlar.
BT Katmanı Elektriksel iletim ve dokunmatik işlevselliği için şeffaf iletken bir film ekler.

Poliimid (PI) Hizalama ve Yönlendirme:Sıvı kristal hizalaması için PI katmanının uygulanması ve yönlendirilmesi.
ODF (Optik Görüntüleme Filmi) görsel efektleri iyileştirir.
Temizlik ve Çerçeve Sızdırmazlık Malzemesi Uygulaması:Sıvı kristal damlacık yerleştirmeye hazırlanıyor.
Sıvı Kristal Enjeksiyonu: Ekrana sıvı kristalin hassas bir şekilde dağıtılması.
TFT ve CF Laminasyon: TFT ve CF bileşenlerinin birbirine bağlanması.
UV Kürleme ve Isıl İşlem:Sıvı kristalin ultraviyole ışık ve ısıl işlemle katılaştırılması ve eşit şekilde dağıtılması.
Kesme, Elektriksel Test ve Kenar Düzeltme:Alt tabakanın şekillendirilmesi, elektrik kontrollerinin yapılması ve kenarların düzeltilmesi.
Polarize Edici Bağlantı ve Kabarcık Giderme: Polarize edici filmlerin uygulanması ve hava kabarcıklarının giderilmesi, gerekirse yeniden işleme izin verilmesi.

Lazer Kesim ve Elektriksel Test:Kesin şekil ve elektriksel bütünlüğün sağlanması.
COG (Cam Üzerindeki Çip) Bağlama, FPC (Esnek Baskılı Devre) Bağlama ve Test:Sürücü devrelerinin kurulumu ve test edilmesi.
Montaj ve Elektriksel Test: Tüm ekran modülü parçalarının birleştirilmesi ve son elektriksel testlerin yapılması.
Yaşlanma: Ürün güvenilirliğini garanti altına almak için uzun vadeli güç kaynağı.
Paketleme ve Kargolama: Bitmiş ürünün teslimata hazırlanması.

Dizi segment akışı
G: SiNx (Silisyum Nitrür) malzemeden yapılmış kapı izolatörü, kapı ile diğer katmanlar arasında gerekli yalıtımı sağlar.
I: Elektronik anahtarlamanın gerçekleştiği kanal katmanı, a-Si (amorf Silisyum).
N: n+ a-Si tabakası yüksek konsantrasyonda Fosfin (PH3) ile katkılanmıştır. Bu katkılama, arayüzdeki potansiyel bariyerini azaltarak güvenilir cihaz çalışması için çok önemli olan Ohmik bir temas sağlar.

Kapı Metali (AlNd/MoN)

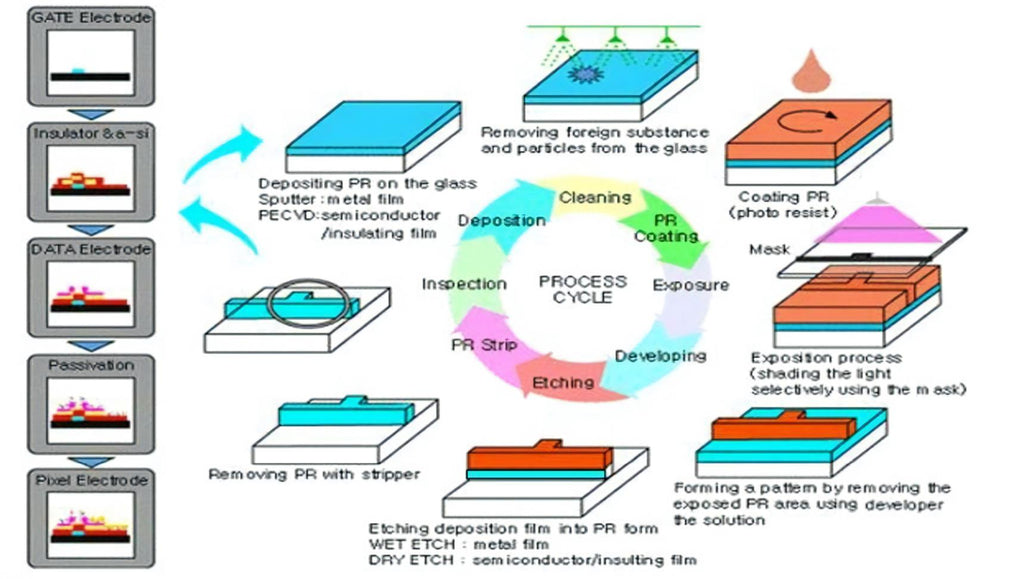
GIN (SiNx / a-Si / n+ a-Si)

S/D Metal (Mo \Al\Mo)
Kaynak ve drenaj elektrotlarının (S/D), veri elektrodunun ve kanalın oluşumu, Molibden Nitrür (MoN) ve saf Alüminyum (kaynak ve drenaj için) ile katmanlama, S/D metal tabakasının püskürtülmesi, S/D fotolitografisi, S/D ıslak aşındırma ve kanal kuru aşındırma gibi özel prosedürleri içerir. Bu işlemlerle, TFT'nin kaynak ve drenaj elektrotları, kanalı ve veri hatları cam alt tabaka üzerinde oluşur. Bu aşamada, TFT'nin yapımı tamamlanır. Ortaya çıkan tasarım ve süreç aşağıdaki gibidir:
S/D Püskürtme: Bu, kaynak/drenaj elektrotları oluşturmak için kritik bir adımdır. Bu işlem sırasında, ağır metal iyonları alt tabakaya püskürtülerek yoğun bir metal elektrot tabakası oluşturulur.
PR Kaplama Öncesi Temizlik: Fotorezist uygulamasından önce, kaplama sonuçlarının iyi olması için, alt tabaka toz ve kalıntılardan arındırılmalıdır.
DHP (Sıcak Plaka): Fotorezistin alt tabakaya daha iyi tutunabilmesi için, kaplama işleminden önce alt tabaka sıcak bir plaka üzerinde önceden ısıtılır.
Direnç Kaplama: Önceden ısıtılmış alt tabakaya, sonraki desenlemede kullanılacak bir fotorezist tabakası uygulanır.
Ön kürleme (SHP):Fotorezist kaplanmış alt tabaka, fotorezistin daha homojen ve daha güçlü olmasını sağlamak için önceden kürlenir.
Adımlayıcı Pozlama:Bu adımda, fotorezistin belirli bölgelerinin sertleştirilmesi ve istenilen desenin oluşturulması için ışık miktarı kontrol edilir.
Gelişmekte: Açığa çıkan fotorezist işlenerek desen ortaya çıkarılır.
Fotorezist Sonrası Pişirme (HHP): Fotorezist deseni daha da sertleştirilir ve başka bir ısıtma işlemiyle daha belirgin hale getirilir. Bu ayrıca kimyasal korozyona ve aşınmaya karşı direnç yeteneğini de artırabilir.
Denetim Geliştirme: Geliştirme sonrasında desenin doğruluğundan emin olmak ve herhangi bir sorunu hemen tespit edip çözmek için detaylı bir inceleme yapılması gerekir.
Islak Aşındırma:Bu, devre desenini oluşturmak için korunmasız bölgelerdeki malzemenin aşındırıcı bir sıvı kullanılarak aşındırıldığı bir kimyasal reaksiyon işlemidir.
Kanal Kuru Aşındırma: Kaynak ve tahliye arasında bir kanal oluşturulur. Bu işlemde kanal bölgesindeki silikon, kuru aşındırma tekniği kullanılarak gerekli şekle aşındırılır.
Direnç Şeridi:Son olarak altlık yüzeyini temizlemek için altlık üzerindeki fotorezist sıyrılır.
Yukarıdaki adımlardan sonra, son olarak cam alt tabaka üzerinde TFT'nin kaynak/drenaj elektrotları, veri elektrotları ve kanalı oluşturulur.
Pasivasyon (SiNx)
Pasivasyon tabakasının (SiNx) oluşumu, genellikle koruyucu yalıtım tabakası olarak bilinir ve geçiş yollarıyla birlikte, PECVD film oluşumu, fotolitografi ve geçiş yolu oluşturma için kuru aşındırma gibi belirli işlemleri içerir. Bu prosedürlerden geçtikten sonra, TFT kanalı ve iletken geçiş yolları için koruyucu yalıtım tabakası son olarak cam alt tabaka üzerinde oluşturulur. Bu adımların tamamlanmasından sonra elde edilen görüntüler ve süreç aşağıdaki gibidir:
2. Kaplama Öncesi Temizlik - Fotorezist uygulamasından önce alt tabakanın temizlendiği yerdir.
3. Sıcak Plaka Ön Pişirme (DHP) - Bu, kaplama adımına hazırlanmak üzere alt tabakayı önceden ısıtmak için bir sıcak plaka kullanılmasını içerir.
4. Fotorezist Kaplama - Bu aşamada alt tabakanın üzerine bir fotorezist tabakası uygulanır.
5. Yumuşak Pişirme (SHP) - Fotorezist ile kaplanan alt tabaka, tabakanın katılaşması için ön kürleme işlemine tabi tutulur.
6. Adımlayıcı Pozlama - Burada fotorezistin açığa çıkarılması ve desenlerin oluşturulması için step litografi teknolojisi kullanılmaktadır.
7. Geliştirme - Açığa çıkarılan fotorezist işlenerek desen ortaya çıkarılır.
8. Sert Pişirme (HHP) - Fotorezist deseni, fırınlama sonrası işlemle sertleştirilir.
9. Geliştirme Sonrası Denetim - Bu aşamada geliştirilen alt tabaka incelenerek desenlerin doğruluğu teyit edilir.
10. Islak Aşındırma - İstenmeyen ince film malzemeleri ıslak kimyasal aşındırma işlemiyle temizlenerek devre desenleri oluşturulur.
11. Fotorezist Soyma - Fotorezist kaldırılır ve alt tabakanın yüzeyi temizlenir.
12. Temas Deliği Aşındırma (CH Aşındırma) - Gerekli delikler kuru aşındırma işlemi ile oluşturulur.
Bunlar, TFT uygulamaları için alt tabakanın hazırlanmasında yer alan ve aktif TFT kanalının korunmasını ve iletken geçişlerin oluşmasını sağlayan ayrıntılı adımlardır.
Şeffaf piksel elektrot ITO'nun (İndiyum-Kalay-Oksit) oluşumu
TFT ekranlarda şeffaf piksel elektrotlarının oluşturulması, İndiyum-Kalay-Oksit (ITO) birikimiyle başlayan karmaşık bir süreçtir. Dahil olan aşamalar hassas bir şekilde tasarlanmıştır ve şeffaflık elde etmek için ITO katmanının püskürtülmesini, ardından karmaşık desenleme için fotolitografiyi ve piksel yapısını sonlandırmak için ıslak aşındırma ile sonlandırmayı içerir. Bu titiz dizi, dizi sürecinin temel tamamlanmasını işaretleyen, cam alt tabakaya kusursuz bir şekilde entegre edilmiş piksel elektrotlarının oluşturulmasıyla sona erer. Aşağıdaki iş akışı, işlem tamamlandıktan sonraki iyileştirme ve işlem sırasını ayrıntılı olarak açıklamaktadır.
Piksel Katman Biriktirme (ITO Püskürtme) – Sonraki piksel desenlemesi için şeffaf bir ITO (İndiyum Kalay Oksit) iletken filmi oluşturur.
Alt Tabaka Temizliği (Ön Direnç Kaplama Temizliği) – Fotorezist malzemesinin uygulanmasından önce alt tabakanın saflığını sağlar.
Substrat Ön Isıtma (Dehidratasyon Sıcak Plakası, DHP) – Optimum fotorezist yapışması için ön pişirme adımıyla alt tabakayı hazırlar.
Direnç Uygulaması (Kaplama) – Alt tabaka üzerine homojen bir fotorezist tabakası uygular.
Yumuşak Pişirme (Ön Kürleme SHP) – Desenlemeden önce fotorezistin katılaşması için ön kürleme gerçekleştirir.
Hassas Pozlama (Adım Adım Pozlama) – Fotorezisti açığa çıkarmak için kademeli fotolitografiyi kullanarak istenilen deseni oluşturur.
Desen Geliştirme (Geliştirme) – Karmaşık piksel desenini ortaya çıkarmak için açığa çıkan fotorezisti geliştirir.
Sertleştirmeye Direnç (Pozlama Sonrası Pişirme, Sert Pişirme HHP) – Desenli fotorezistin aşınma direncini artırmak için sertleştirir.
Desen Denetimi (Geliştirme Sonrası Denetim) – Geliştirilen desenlerin doğruluğunu ve bütünlüğünü denetler.
Desen Transferi (ITO Aşındırma) – ITO tabakasını aşındırarak deseni piksel elektrotlar oluşturacak şekilde aktarır.
Direnç Kaldırma (Şerit) – Fotorezisti sıyırarak temiz bir alt tabaka yüzeyi bırakır.
Performans Arttırma (Tavlama) – İnce film transistörlerin elektriksel özelliklerini iyileştirmek için bileşenleri tavlar.
Kalite Kontrol (TEG Testi) – Üretim sırasında kaliteyi izlemek için test elemanlarında elektriksel testler gerçekleştirir.
Bu akıcı dizilim, optimum elektriksel performansa sahip yüksek kaliteli TFT ekranlar için temel oluşturuyor.

Renk Filtresi (CF) işlemi
Cam Alt Tabaka: Mekanik desteği sağlayan temel taban katmanı.
Kara Matris (BM): Işığı emen bir malzemeden yapılmış olup, her bir pikseli belirginleştirir ve pikseller arası ışık sızıntısını en aza indirerek kontrastı artırır.
Renkli Reçine Katmanları: Gerçek kırmızı, yeşil ve mavi renkli filtreler olarak, bu katmanlar piksel renklerini belirler. Boyalı şeffaf reçine malzemeden üretilirler.
Üst Katman (OC): Filtreleri fiziksel ve kimyasal hasarlardan korumak ve yüzeyi eşitlemek için renkli reçinelerin üzerine uygulanan koruyucu bir tabaka.
ITO (İndiyum Kalay Oksit) Elektrot: Bu şeffaf iletken tabaka, panelin bir elektrot gibi çalışmasını sağlayarak içinden geçen ışığın düzenlenmesini sağlar.

Alt Tabaka Hazırlığı: Cam alt tabakanın temizliği son derece önemlidir, bu nedenle CF kalitesini tehlikeye atabilecek kirlilikleri ortadan kaldırmak için kapsamlı bir temizlikten geçirilir.
Siyah Matris Oluşumu: Temizlenmiş alt tabakaya bir fotorezist tabakası uygulanarak, BM desenini ana hatlarıyla belirtmek için fotolitografi kullanılır. Pozlamadan sonra, gelişmemiş alanlar ortaya çıkarılır ve siyah pigmentle doldurulur, ardından kürlenir.
Renkli Reçine Uygulaması: BM sınırları içinde kırmızı, yeşil ve mavi renkli reçinelerin ardışık uygulaması, her renk katmanı için ayrı bir fotolitografi işlemi kullanılarak gerçekleştirilir. Kaplama ve pozlamadan sonra, fotorezist olmayan alanlar geliştirilir ve reçine ile doldurulur, ardından kürleme yapılır.
Palto Katmanı Uygulaması: Reçine renklerinin üzerine, onları korumak ve sonraki ITO elektrot birikimi için pürüzsüz bir yüzey oluşturmak amacıyla bir OC tabakası uygulanır.
ITO Elektrot Birikimi: Şeffaf ITO elektrot, OC tabakasının üzerine püskürtme yoluyla biriktirilir ve daha sonra elektrot mimarisini yapılandırmak için desenlendirilir.
Muayene ve Test: Üretim boyunca titiz incelemeler ve testler CF kalitesini garanti eder. Renk doğruluğu, tekdüzelik ve kusur seviyeleri gibi ölçümler kapsamlı bir şekilde incelenir.
Entegrasyon: Kalite güvencesinden sonra, Renkli Filtre hassas bir şekilde hizalanır ve TFT dizisi ve sıvı kristal katmanı gibi TFT-LCD panel bileşenleri ile lamine edilir.

HÜCRE Segment Akışı
Bir TFT ekranının 'Hücre' yönü içindeki üretim süreci kabaca dört temel aşamaya ayrılabilir: Hizalama, Kutulama, Kesme ve Polarize Edici Bağlantı. Bu aşamaların hedefleri ve birincil prosedürleri kısaca aşağıdaki gibi özetlenmiştir:
Hizalama Süreci
Hizalama sürecinin amacı, hem TFT hem de CF alt tabakalarında şeffaf bir PI (Polimid) film tabakası oluşturmaktır. Daha sonraki bir sürtünme süreciyle, bu tabaka sıvı kristal moleküllerinin sürtünme yönünde hizalanmasını etkiler. Altta yatan prensiplerin daha derin bir şekilde anlaşılması için, ilgili okuyucular ilgili literatüre başvurmalıdır. Bu nedenle, bu aşama belirgin bir şekilde iki temel süreci içerir: PI Baskı ve Sürtme.
PI(Polimid)Baskı
Poliimid (PI), ana ve yan zincirlerden oluşan yüksek performanslı, şeffaf bir organik polimer malzemedir. Uygulama ve pişirme sonrasında CF ve TFT alt tabakalarının yüzeylerine sıkıca yapışır. PI kaplaması özel bir gravür baskı tekniği kullanır. Birincil gravür baskı işleminin yanı sıra, PI baskı, baskıdan önce alt tabaka temizliği, baskıdan sonra ön pişirme, otomatik optik inceleme, kürleme ve gerekirse bir PI yeniden işleme işlemi dahil olmak üzere çeşitli yardımcı işlemleri içerir.
1. Ön-PI Temizliği:Bu adım, baskıdan önce alt tabakanın iyice temizlenmesini, toz, gres ve diğer kirleticilerden arındırılmasını ve bir sonraki adımlara hazırlanmasını içerir.
2.PI Baskı:Burada, PI (Poliimid) malzemesi, kağıt üzerine bir tasarım basmaya benzer şekilde, alt tabakaya uygulanır; ancak 'mürekkep', koruyucu bir tabaka oluşturan özel bir malzemedir.3.Ön Pişirme:Bunu, PI katmanının alt tabakaya düzgün bir şekilde yapışmasını sağlamak için kısmen kuruduğu ön bir pişirme aşaması olarak düşünün.
4.PI Denetimi:Bu noktada, basılı katmanlar, boyalı bir duvarda kusur olup olmadığının incelenmesine benzer şekilde, lekeler, düzensiz alanlar veya kusurlar açısından yakından incelenir.
5.PI Yeniden Çalışma:Eğer inceleme sırasında herhangi bir sorun tespit edilirse, bu adım, bir eskizdeki hataları silmeye benzer şekilde, söz konusu kusurların düzeltilmesini gerektirir.
6.PI Kürleme:Son olarak, PI tabakası tıpkı kilin fırında sertleştirilmesi gibi bir pişirme işlemiyle tamamen sertleştirilir ve bu da onu güçlü ve dayanıklı hale getirir.
Bu aşama, kapsamlı temizlik için ultrasonik dalgalar kullanan bir ultrasonik temizleyici kullanarak alt tabakadan toz ve parçacıkları temizlemeyi amaçlar. Bu, bir sonraki adımlara geçmeden önce alt tabakanın herhangi bir kirleticiden arındırılmasını sağlar.
2. Hizalama:
Hizalama aşaması, görsel gereksinimleri karşılamak için alt tabakanın yönelimini ayarlar. Bu süreç basittir ve alt tabakanın sonraki işlemler için doğru şekilde konumlandırılmasına odaklanır.
3. Sürtünme:
Sürtünme aşamasında, kadife bir bez PI tabakasının üzerine sürtünerek kullanılır. Bu eylem, PI'nin yan zincirlerini birleşik bir yönde hizalayarak, istenen yüzey özelliklerini elde etmek için moleküler yapıyı düzenler.
4. Sürtünme Sonrası Ultrasonik Temizleme (USC):
Ovma işleminden sonra, alt tabakada partikül madde veya kalıntılar olabilir. Ovma sonrası USC temizliği bu kalıntıları temizleyerek alt tabakanın yüzeyinin kusursuz bir şekilde temiz olmasını sağlar. Bu adım, ovma işlemi sırasında yapışan parçacıkları veya kalıntıları çıkarmak ve çıkarmak için ultrasonik dalgalar kullandığından, nihai ürünün kalitesini korumak için kritik öneme sahiptir.

ODF(One Drop Fill) Kapsülleme İşlemi
1. Sızdırmazlık Maddesi ve Gümüş Macun Uygulaması:UV ile kürlenen yapıştırıcı, iki alt tabakanın sıkıca bağlanmasını ve hücrenin kalınlığını belirlemek için CF ve TFT cam alt tabakalarının kenarlarına uygulanan sızdırmazlık maddesi olarak kullanılır. Aynı anda, gümüş macunun uygulanması, elektriksel bağlantıyı sağlamak için CF ve TFT üzerindeki ortak elektrotları bağlamak içindir.
2. Sıvı Kristal Kaplama:Sıvı kristal malzeme, sızdırmazlık maddesiyle kaplanmış olan TFT alt tabakasına damlatılır. Sıvı kristal malzeme, görüntüleme sürecinde kritik bir rol oynar; düzenlemesini değiştirerek içinden geçen ışığın durumunu ayarlar ve böylece piksellerin rengini ve parlaklığını kontrol eder.
3. Vakumla Bağlama:Sızdırmazlık maddesi, gümüş macun ve sıvı kristal ile kaplanmış CF alt tabakası, vakum ortamında TFT alt tabakasına bağlanır. Bu adım, kabarcık oluşumunu önlemeye yardımcı olur ve iki alt tabaka arasında sıkı, boşluksuz bir bağ olmasını sağlar.
Isıl Kürleme:UV kürleme tamamlandıktan sonra, alt tabakalar sızdırmazlık maddesinin yapışmasını daha da güçlendirmek için termal bir işlemden geçirilir. Bu adım özellikle UV ışığının tam olarak ulaşamadığı, örneğin kabloların altındaki alanları hedef alır ve bu parçaların iyice kürlenmesini sağlar.

1.Kesme
Cam alt tabakanın belirli boyutu ve ürün boyutlarındaki çeşitlilik nedeniyle, birden fazla ürün hücresi tek bir cam alt tabaka üzerinde düzenlenir. Kesme, elmas bir tekerleğin cam yüzeyinde kaydırılmasıyla gerçekleştirilir. Genellikle kesme işleminden sonra bir ayırma işlemi olur, ancak kesme tekerleği teknolojisindeki gelişmelerle artık çok derin bir kesim izi oluşturan ve ayırma ihtiyacını ortadan kaldıran bir teknik bulunmaktadır.
2.Kenar
Cam ayrı ayrı ekranlara kesildikten sonra, her ekranın kenarlarında çok sayıda ince çatlak bulunur. Bu çatlakların daha sonraki taşımalarda çarpışmalar nedeniyle kırılmaya neden olmasını önlemek için kenar işlemi gereklidir.
3.Elektriksel Ölçüm
Elektriksel ölçüm, üretim sırasında birden fazla kez kullanılan yardımcı bir işlemdir, ancak burada özellikle önemlidir çünkü bu, LCD'nin ekran performansını test etmek için elektriğin ilk kez uygulandığı zamandır. Test prensibi basittir: elektriği ayrı ekran piksellerine uygulayın ve hücrenin ekran performansını polarize edici bir film aracılığıyla gözlemleyin. Genellikle, dizi testi için kullanılan kısa bir çubuk elektriklendirilir. Elektriksel testten sonra, standartları karşılamayan ekranlar, daha sonraki aşamalarda malzeme israfını önlemek için kaldırılır.
Kesim sonrası görsel inceleme ve kenar temizliği de ek yardımcı süreçler arasındadır.
TFT Ekran Modülü Montaj Süreci
TFT ekran modüllerinin montajında yer alan birincil süreçler arasında polarize edici filmin uygulanması, COG ve FPC bağlama, montaj ve çeşitli destekleyici süreçler yer alır. Aşağıda her birine ilişkin ayrıntılı bir giriş bulunmaktadır:
1.COG ve FPC Bağlama
COG (Cam Üzerindeki Çip) ve FPC (Esnek Baskılı Devre), devreleri bağlama yöntemlerini temsil eder. Çok sayıda elektrot nedeniyle, geleneksel bire bir tel bağlantıları zordur. Mevcut uygulama, IC/FPC üzerinde karşılık gelen bir diziyle cam üzerinde bir elektrot dizisi oluşturmayı ve her IC/FPC elektrodunu cam elektroda tek tek bağlamak için Anizotropik İletken Film (ACF) kullanmayı içerir.2. Polarize Filmin Uygulanması
LCD çalışması polarize ışığa dayandığından, polarize edici bir filmin eklenmesi önemli bir işlemdir. Bu film, görüntü üretmek için sıvı kristal hücrelerinden geçen ışığı kontrol eder.
3.Montaj
Montaj, arka aydınlatmayı, ekranı, kontrol devre kartını ve dokunmatik ekranlar gibi diğer bileşenleri bir araya getirerek eksiksiz bir ekran modülü oluşturur. Bu genellikle, monte edilen modüllerin kalitesini sağlamada önemli bir rol oynayan yetenekli teknisyenler tarafından manuel olarak yapılır.
Modül segmenti ana proseslere ek olarak aşağıdaki gibi çeşitli yardımcı prosesleri de içerir:
1.Lazer Kesim ve Kesim Sonrası Elektrik Ölçümü
Parçalar lazer kullanılarak hassas bir şekilde kesildikten sonra, gerekli özellikleri karşıladıklarından emin olmak için elektriksel fonksiyonları test edilir.2.Bağlama ve Bağlama Sonrası Elektrik Ölçümü
COG ve FPC birleştirme işlemlerinden sonra bu bağlantıların sağlamlığını doğrulamak amacıyla elektriksel testler de yapılır.
3.Mikroskobik Muayene
Lazer kesim ve yapıştırma işleminden sonra, herhangi bir kusur veya sorun olup olmadığını kontrol etmek için mikroskobik incelemeler (veya FPC yapıştırma işlemi için Otomatik Optik İnceleme (AOI)) gerçekleştirilir.
4. Soyulma Mukavemeti Testi
IC yapıştırma ve FPC yapıştırma işlemlerinden sonra, yapıştırmaların dayanıklılığını değerlendirmek amacıyla soyulma dayanımı testleri yapılır.
5.Montaj Sonrası Yaşlanma
Birleştirilen modüller, uzun vadeli güvenilirliği garanti altına almak için güç uygulanan bir yaşlanma sürecinden geçirilir.
6. Paketleme ve Sevkiyat
Modüller tüm test ve muayenelerden geçtikten sonra paketlenerek müşteriye veya üretim sürecinin bir sonraki aşamasına gönderilir.
