
A estrutura do display TFT LCD
Painel de Cristal Líquido (Painel): Esta é a parte principal do display, responsável por apresentar a imagem. O painel de cristal líquido é formado por duas placas de vidro com uma camada de cristal líquido intercalada entre elas, conhecida como célula de cristal líquido.
Filtros polarizadores:Esses componentes estão localizados em ambos os lados da célula de cristal líquido e têm a tarefa de processar a luz que passa pela célula.
Filtro de cor: Geralmente fabricado em uma das placas de vidro da célula de cristal líquido selada, é usado para exibição de cores.
Matriz de transistores de película fina (matriz TFT): Posicionado na outra placa de vidro da célula de cristal líquido selada, ele desempenha um papel ativo no acionamento do display.
Luz de fundo:A fonte de luz localizada atrás do módulo de exibição TFT-LCD fornece a luz necessária para que a imagem visível seja produzida através da célula de cristal líquido.
Circuito de acionamento externo:Esses circuitos são responsáveis por gerenciar os sinais de imagem de entrada para acionar adequadamente o conjunto TFT e a luz de fundo.

O processo de fabricação de displays TFT LCD
Formação de Filme:Técnicas como pulverização catódica (SPT) e deposição química de vapor (CVD) depositam múltiplas camadas no substrato.
Fotolitografia:Aplicação, exposição e revelação de fotorresistentes para formar microestruturas.
Gravura:Os métodos de gravação úmida e seca esculpem o substrato removendo áreas específicas.
Decapagem: Após a padronização, o excesso de materiais é removido para limpar o substrato.
Etapas do processo auxiliar:
Limpeza:Garante que o substrato esteja livre de contaminação.
Marcação e Exposição:Identifica e prepara as bordas do substrato.
Inspeção Óptica Automatizada (AOI):Usado para inspeção de defeitos.
Inspeção Microscópica e Inspeção Macroscópica (Mic/Mac):Verificação de detalhes.
Teste de desempenho do filme:Utiliza ferramentas como medidores de resistência de chapas, perfilômetros, refletômetros/elipsometrias, espectroscopia de infravermelho com transformada de Fourier.
Teste elétrico aberto/curto (O/S):Verifica a continuidade do circuito e curtos. Teste elétrico do grupo de elementos de teste (TEG): testa o desempenho elétrico dos elementos.
Teste elétrico de matriz:Garante a funcionalidade elétrica do conjunto.
Reparo a Laser:Corrige quaisquer defeitos de acordo com os resultados da inspeção.
Retrabalho de fotorresistência (retrabalho de RP):Ajusta ou repete as etapas da fotolitografia, se necessário.
Retrabalho de filme: altera ou aperfeiçoa o processo de formação do filme, se necessário.

Camada OC protege e prepara os padrões do filtro de cor.
Camada RGB formação por meio de sequências de revestimento, exposição e desenvolvimento.
Camada BM (Black Matrix) melhora o contraste e limita o vazamento de luz.
Camada PS (espaçador de fotos) mantém um espaço preciso entre os substratos, crucial para a qualidade da imagem.
ESTA Camada adiciona uma película condutora transparente para condução elétrica e funcionalidade de toque.

Alinhamento e orientação de poliimida (PI): Aplicando e orientando a camada PI para alinhamento de cristal líquido.
ODF (Filme de exibição óptica) melhora os efeitos visuais.
Limpeza e aplicação de selante de estrutura: Preparando para inserção de gotículas de cristal líquido.
Injeção de Cristal Líquido:Distribuição precisa do cristal líquido no display.
Laminação TFT e CF: União dos componentes TFT e CF.
Cura UV e processamento térmico: Solidificação e distribuição uniforme do cristal líquido com luz ultravioleta e tratamento térmico.
Corte, Testes Elétricos e Suavização de Bordas: Moldar o substrato, realizar verificações elétricas e suavizar bordas.
Fixação do polarizador e remoção de bolhas: Aplicação de filmes polarizadores e eliminação de bolhas de ar, sendo permitido retrabalho se necessário.

Corte a laser e testes elétricos: Garantindo forma precisa e integridade elétrica.
Colagem COG (Chip On Glass), Colagem FPC (Circuito Impresso Flexível) e Testes:Instalação e teste do circuito de acionamento.
Montagem e Testes Elétricos: Combinando todas as peças do módulo de exibição e realizando os testes elétricos finais.
Envelhecimento: Fonte de alimentação de longo prazo para garantir a confiabilidade do produto.
Embalagem e Envio: Preparando o produto acabado para entrega.

Fluxo de segmento de matriz
G: O isolador da comporta, feito de SiNx (nitreto de silício), fornece o isolamento necessário entre a comporta e outras camadas.
I: A camada do canal, a-Si (Silício amorfo), onde ocorre a comutação eletrônica.
N: A camada n+ a-Si é dopada com uma alta concentração de Fosfina (PH3). Essa dopagem reduz a barreira de potencial na interface, garantindo um contato ôhmico que é crucial para a operação confiável do dispositivo.

Portão metálico (AlNd/MoN)

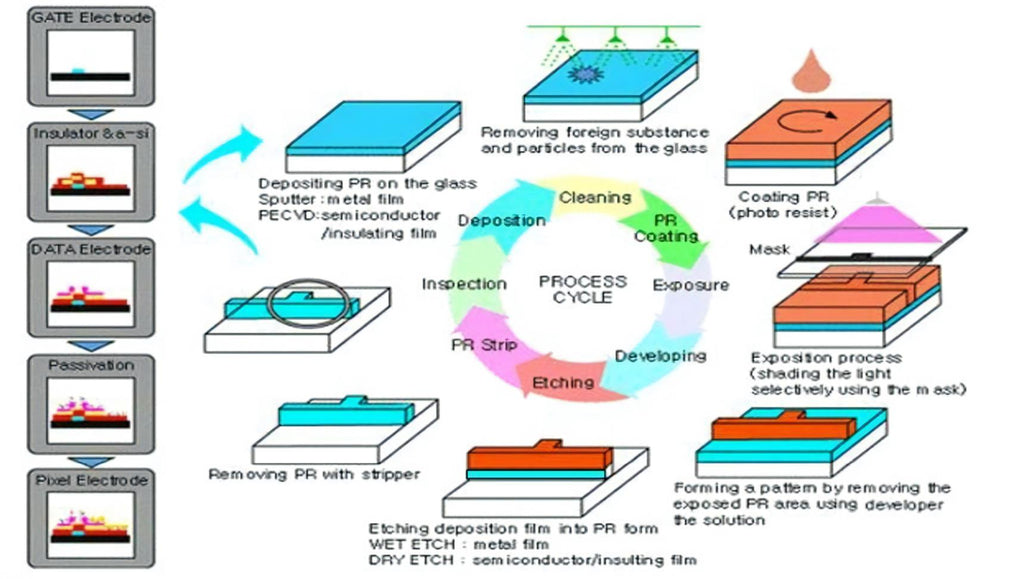
GIN (SiNx / a-Si / n+ a-Si)

Metal S/D (Mo \ Al \ Mo)
A formação dos eletrodos de fonte e dreno (S/D), eletrodo de dados e canal inclui procedimentos específicos, como camadas com nitreto de molibdênio (MoN) e alumínio puro (para fonte e dreno), pulverização catódica da camada de metal S/D, fotolitografia S/D, gravação úmida S/D e gravação seca de canal. Por meio desses processos, os eletrodos de fonte e dreno, canal e linhas de dados do TFT se formam no substrato de vidro. Nesta fase, a construção do TFT é concluída. O design e o processo resultantes são os seguintes:
Pulverização S/D: Esta é uma etapa crucial para formar eletrodos de fonte/dreno. Durante este processo, uma camada densa de eletrodos de metal é formada por pulverização catódica de íons de metais pesados no substrato.
Limpeza antes do revestimento PR: Antes de aplicar o fotorresistente, o substrato deve ser limpo para remover poeira e resíduos, garantindo bons resultados de revestimento.
DHP (Placa Quente): Para melhor fixação do fotorresistente ao substrato, o substrato é pré-aquecido em uma chapa quente antes do processo de revestimento.
Revestimento de resistência: Aplique uma camada de fotorresistente ao substrato pré-aquecido, que será usado para a padronização subsequente.
Pré-cura (SHP): O substrato revestido com fotorresistente é pré-curado para torná-lo mais uniforme e forte.
Exposição de Stepper:Nesta etapa, a quantidade de exposição à luz é controlada para endurecer certas áreas do fotorresistente e criar o padrão desejado.
Em desenvolvimento: O fotorresistente exposto é processado para revelar o padrão.
Pós-cozimento de fotorresistência (HHP): O padrão fotorresistente é ainda mais endurecido e se torna mais proeminente por meio de outro processo de aquecimento. Isso também pode melhorar sua capacidade de resistir à corrosão química e ao desgaste.
Inspeção em desenvolvimento:Após o desenvolvimento, uma inspeção detalhada é necessária para garantir a precisão do padrão e detectar e resolver prontamente quaisquer problemas.
Gravura úmida:Este é um processo de reação química em que um líquido corrosivo é usado para gravar o material nas áreas não protegidas para formar o padrão do circuito.
Canal de gravação a seco: Um canal é formado entre a fonte e o dreno. Neste processo, o silício na região do canal é gravado no formato necessário usando uma técnica de gravação a seco.
Tira de resistência:Finalmente, para limpar a superfície do substrato, o fotorresistente do substrato é removido.
Após as etapas acima, os eletrodos de fonte/dreno, eletrodos de dados e canal de TFT são finalmente formados no substrato de vidro.
Passivação (SiNx)
A formação da camada de passivação (SiNx), frequentemente conhecida como camada de isolamento protetor, juntamente com as vias, inclui operações específicas, como formação de filme PECVD, fotolitografia e gravação a seco para criação de via. Após passar por esses procedimentos, a camada de isolamento protetor para o canal TFT e as vias condutoras são finalmente formadas no substrato de vidro. As imagens e o processo obtidos após a conclusão dessas etapas são os seguintes:
2. Limpeza de pré-revestimento - É aqui que o substrato é limpo antes da aplicação do fotorresistente.
3. Pré-cozimento na chapa quente (DHP) - Isso envolve o uso de uma placa de aquecimento para pré-aquecer o substrato e prepará-lo para a etapa de revestimento.
4. Revestimento fotorresistente - Uma camada de fotorresistente é aplicada sobre o substrato durante esta etapa.
5. Assar macio (SHP) - O substrato, revestido com fotorresistente, passa por um processo de pré-cura para solidificar a camada.
6. Exposição do Stepper - Aqui, a tecnologia de litografia passo a passo é usada para expor a fotorresistência e formar padrões.
7. Desenvolvimento - O fotorresistente exposto é processado para revelar o padrão.
8. Cozimento Duro (HHP) - O padrão fotorresistente é endurecido por meio de um tratamento pós-cozimento.
9. Inspeção pós-desenvolvimento - Esta etapa envolve a inspeção do substrato desenvolvido para confirmar a precisão dos padrões.
10. Gravura úmida - Materiais de película fina indesejados são removidos por meio de um processo de corrosão química úmida para criar padrões de circuito.
11. Decapagem de fotorresistência - O fotorresiste é removido e a superfície do substrato é limpa.
12. Gravação de furos de contato (CH Etching) - As vias necessárias são formadas por meio de um processo de gravação a seco.
Estas são as etapas detalhadas envolvidas na preparação do substrato para aplicações TFT, levando à proteção do canal TFT ativo e à formação de vias condutoras.
Formação de eletrodo de pixel transparente ITO (óxido de índio-estanho)
A criação de eletrodos de pixel transparentes em displays TFT é um processo sofisticado, começando com a deposição de Óxido de Índio-Estanho (ITO). Os estágios envolvidos são projetados com precisão e incluem pulverização catódica da camada de ITO para obter transparência, seguido por fotolitografia para padrões intrincados e concluído com gravação úmida para finalizar a estrutura do pixel. Esta sequência meticulosa conclui com a formação dos eletrodos de pixel, perfeitamente integrados ao substrato de vidro, marcando a conclusão fundamental do processo de matriz. O fluxo de trabalho a seguir detalha o refinamento e a sequência de operações pós-conclusão do processo.
Deposição de camada de pixel (ITO Sputtering) – Estabelece uma película condutora transparente de ITO (óxido de índio e estanho) para posterior padronização de pixels.
Limpeza de substrato (limpeza de revestimento pré-resistente) – Garante a pureza do substrato antes da aplicação do material fotorresistente.
Pré-aquecimento do substrato (placa de desidratação, DHP) – Prepara o substrato com uma etapa de pré-cozimento para ótima adesão do fotorresistente.
Aplicação de resistência (revestimento) – Aplica uma camada uniforme de fotorresistente no substrato.
Soft Bake (Pré-cura SHP) – Realiza pré-cura para solidificar o fotorresistente antes da padronização.
Exposição de precisão (exposição de passo) – Utiliza fotolitografia de passo para expor o fotorresistente, criando o padrão desejado.
Desenvolvimento de Padrões (Desenvolvimento) – Desenvolve o fotorresistente exposto para revelar o intrincado padrão de pixels.
Resist Harden (cozimento pós-exposição, cozimento duro HHP) – Endurece o fotorresistente padronizado para melhorar a resistência à corrosão.
Inspeção de padrões (inspeção pós-desenvolvimento) – Inspeciona os padrões desenvolvidos quanto à precisão e integridade.
Transferência de padrões (gravação ITO) – Transfere o padrão através da gravação da camada ITO para formar eletrodos de pixel.
Remoção de resistência (tira) – Remove o fotorresistente, deixando uma superfície de substrato limpa.
Melhoria de desempenho (recozimento) – Recoze os componentes para melhorar as propriedades elétricas dos transistores de película fina.
Controle de Qualidade (Teste TEG) – Realiza testes elétricos em elementos de teste para monitorar a qualidade durante a produção.
Esta sequência simplificada estabelece as bases para displays TFT de alta qualidade com desempenho elétrico ideal.

Processo de filtro de cor (CF)
Substrato de vidro: A camada base fundamental que fornece suporte mecânico.
Matriz Negra (BM): Constituído de um material que absorve a luz, ele delineia cada pixel e minimiza o vazamento de luz entre pixels, melhorando o contraste.
Camadas de resina colorida: Como os filtros vermelhos, verdes e azuis reais, essas camadas determinam as cores dos pixels. Elas são criadas a partir de um material de resina transparente tingido.
Camada de Sobrecapa (OC): Uma camada protetora sobreposta às resinas coloridas para uniformizar a superfície e proteger os filtros de danos físicos e químicos.
Eletrodo ITO (óxido de índio e estanho): Essa camada condutora transparente permite que o painel opere como um eletrodo, regulando a luz que passa por ele.

Preparação do substrato: A limpeza do substrato de vidro é primordial, por isso ele passa por uma limpeza completa para erradicar impurezas que podem comprometer a qualidade do CF.
Formação da Matriz Negra: Aplicando uma camada de fotorresistência ao substrato limpo, a fotolitografia é utilizada para delinear o padrão BM. Após a exposição, áreas não reveladas são reveladas e preenchidas com pigmento preto, então curadas.
Aplicação de resina colorida: A aplicação sucessiva de resinas de cor vermelha, verde e azul dentro dos limites do BM é realizada usando um processo de fotolitografia distinto para cada camada de cor. Após o revestimento e a exposição, as áreas sem fotorresistência são reveladas e preenchidas com a resina, seguidas pela cura.
Aplicação da camada de sobrecapa: Uma camada de OC é aplicada sobre as cores de resina para protegê-las e estabelecer uma superfície lisa para a posterior deposição do eletrodo ITO.
Deposição de eletrodos ITO: O eletrodo ITO transparente é depositado por pulverização catódica na camada OC e então padronizado para estruturar a arquitetura do eletrodo.
Inspeção e Teste: Durante toda a produção, inspeções e testes meticulosos garantem a qualidade CF. Métricas como fidelidade de cor, uniformidade e níveis de defeito são examinados minuciosamente.
Integração: Após a garantia de qualidade, o filtro de cor é precisamente alinhado e laminado com componentes do painel TFT-LCD, como a matriz TFT e a camada de cristal líquido.

Fluxo do segmento CELL
O processo de produção dentro do aspecto 'Cell' de um display TFT pode ser dividido em quatro estágios principais: Alinhamento, Boxing, Corte e Fixação do Polarizador. Os objetivos e procedimentos primários desses estágios são resumidos a seguir:
O Processo de Alinhamento
O objetivo do processo de Alinhamento é criar uma camada de filme transparente de PI (Poliimida) nos substratos TFT e CF. Por meio de um processo de fricção subsequente, essa camada influencia as moléculas de cristal líquido a se alinharem na direção da fricção. Para uma compreensão mais profunda dos princípios subjacentes, os leitores interessados devem consultar a literatura relevante. Portanto, esse estágio apresenta com destaque dois processos primários: Impressão e fricção de PI.
Impressão de PI (Poliimida)
Poliimida (PI) é um material de polímero orgânico transparente de alto desempenho que consiste em cadeias principais e laterais. Após a aplicação e cozimento, ele adere firmemente às superfícies de substratos CF e TFT. O revestimento de PI utiliza uma técnica especial de impressão em rotogravura. Além do processo primário de impressão em rotogravura, a impressão em PI envolve vários processos auxiliares, incluindo limpeza do substrato antes da impressão, pré-cozimento após a impressão, inspeção óptica automática, cura, bem como um processo de retrabalho de PI, se necessário.
1.Limpeza pré-PI:Esta etapa envolve a limpeza completa do substrato antes da impressão, garantindo que ele esteja livre de poeira, graxa e outros contaminantes para prepará-lo para as próximas etapas.
2. Impressão PI:Aqui, o material PI (poliimida) é aplicado ao substrato, de forma análoga à impressão de um desenho no papel, exceto que a "tinta" é um material especial que forma uma camada protetora.3. Pré-cozimento:Considere esta uma fase de cozimento preliminar, que seca parcialmente a camada de PI para garantir a adesão adequada ao substrato.
4. Inspeção de PI:Nesse ponto, as camadas impressas passam por um exame minucioso para detectar manchas, áreas irregulares ou defeitos, semelhante à inspeção de uma parede pintada em busca de imperfeições.
5. Retrabalho de PI:Se algum problema for identificado durante a inspeção, esta etapa envolve a correção dessas imperfeições, semelhante a apagar erros em um esboço.
6. Cura de PI:Finalmente, a camada de PI é totalmente endurecida por meio de um processo de cozimento, assim como a argila é endurecida em um forno, o que a torna forte e durável.
Esta etapa tem como objetivo remover poeira e partículas do substrato usando um limpador ultrassônico, que emprega ondas ultrassônicas para limpeza completa. Isso garante que o substrato esteja livre de quaisquer contaminantes antes de prosseguir para as próximas etapas.
2. Alinhamento:
A fase de alinhamento ajusta a orientação do substrato para atender aos requisitos visuais. Esse processo é direto, focando no posicionamento correto do substrato para tratamentos subsequentes.
3. Esfregar:
Durante o estágio de fricção, um pano de veludo é usado para esfregar sobre a camada de PI. Essa ação alinha as cadeias laterais do PI em uma direção unificada, organizando a estrutura molecular para atingir as propriedades de superfície desejadas.
4. Limpeza ultrassônica pós-fricção (USC):
Após a fricção, o substrato pode ter partículas ou resíduos. A limpeza USC pós-fricção remove esses resíduos, garantindo que a superfície do substrato esteja impecavelmente limpa. Esta etapa é crítica para manter a qualidade do produto final, pois usa ondas ultrassônicas para desalojar e remover quaisquer partículas ou resíduos aderidos durante o processo de fricção.

Processo de encapsulamento ODF (One Drop Fill)
1. Aplicação de selante e pasta de prata:O adesivo curável por UV é usado como selante, aplicado ao longo das bordas dos substratos de vidro CF e TFT, para garantir que os dois substratos estejam firmemente unidos e para definir a espessura da célula. Simultaneamente, a aplicação de pasta de prata é para conectar os eletrodos comuns em CF e TFT para garantir a conectividade elétrica.
2. Revestimento de cristal líquido:O material de cristal líquido é jogado no substrato TFT que já foi revestido com o selante. O material de cristal líquido desempenha um papel crítico no processo de exibição; ele ajusta o estado da luz que passa alterando seu arranjo, controlando assim a cor e o brilho dos pixels.
3. Colagem a vácuo:O substrato CF, que foi revestido com o selante, pasta de prata e cristal líquido, é colado com o substrato TFT em um ambiente de vácuo. Esta etapa ajuda a evitar a formação de bolhas e garante que haja uma ligação firme e sem lacunas entre os dois substratos.
Cura térmica:Após a cura UV ser concluída, os substratos passam por um processo térmico para fortalecer ainda mais a adesão do selante. Esta etapa é particularmente voltada para áreas não totalmente atingidas pela luz UV, como sob os fios, garantindo que essas partes sejam completamente curadas.

1. Corte
Devido ao tamanho definido do substrato de vidro e à variedade de tamanhos de produtos, várias células de produtos são organizadas em um único substrato de vidro. O corte é realizado deslizando uma roda de diamante pela superfície do vidro. Normalmente, há um processo de descolamento após o corte, mas com os avanços na tecnologia de rodas de corte, agora há uma técnica que cria uma marca de corte muito profunda, eliminando a necessidade de descolamento.
2. Borda
Após o vidro ser cortado em telas individuais, as bordas de cada tela apresentam muitas rachaduras finas. Para evitar que essas rachaduras causem quebra devido a colisões no manuseio subsequente, é necessário um tratamento de bordas.
3. Medição elétrica
A medição elétrica é um processo auxiliar usado várias vezes durante a produção, mas é especialmente crucial aqui, pois esta é a primeira vez que a eletricidade é aplicada para testar o desempenho do display do LCD. O princípio do teste é simples: aplique eletricidade a pixels individuais do display e observe o desempenho do display da célula por meio de um filme polarizador. Normalmente, uma barra curta usada para teste de matriz é eletrificada. Após o teste elétrico, as telas que não atendem aos padrões são removidas para evitar desperdício de materiais em estágios posteriores.
Processos auxiliares adicionais incluem inspeção visual pós-corte e limpeza pós-afiação.
Processo de montagem do módulo de exibição TFT
Os processos primários envolvidos na montagem de módulos de display TFT incluem a aplicação do filme polarizador, colagem de COG e FPC, montagem e vários processos de suporte. Abaixo está uma introdução detalhada a cada um:
1. Ligação COG e FPC
COG (Chip on Glass) e FPC (Flexible Printed Circuit) representam métodos de conexão de circuitos. Devido à multiplicidade de eletrodos, as conexões tradicionais de fio um-para-um são desafiadoras. A prática atual envolve a formação de uma matriz de eletrodos no vidro, com uma matriz correspondente no IC/FPC, e o uso de Anisotropic Conductive Film (ACF) para conectar cada eletrodo IC/FPC com o eletrodo de vidro, um por um.2.Aplicando o filme polarizador
Como a operação do LCD é baseada em luz polarizada, a fixação de um filme polarizador é um processo essencial. Este filme controla a luz que passa pelas células de cristal líquido para produzir imagens.
3.Montagem
A montagem reúne a luz de fundo, a tela, a placa de circuito de controle e outros componentes como telas sensíveis ao toque para formar um módulo de exibição completo. Isso é feito normalmente manualmente por técnicos qualificados, que desempenham um papel crucial em garantir a qualidade dos módulos montados.
Além dos processos principais, o segmento de módulos inclui vários processos auxiliares, como:
1.Corte a laser e medição elétrica pós-corte
Depois que os componentes são cortados com precisão usando um laser, suas funções elétricas são testadas para garantir que atendam às especificações exigidas.2. Medição elétrica de ligação e pós-ligação
Testes elétricos também são realizados após os processos de ligação COG e FPC para verificar a integridade dessas conexões.
3. Inspeção Microscópica
Após o corte e a colagem a laser, são realizadas inspeções microscópicas (ou Inspeção Óptica Automatizada (AOI) para colagem de FPC) para verificar se há defeitos ou problemas.
4. Teste de resistência à casca
Após a colagem IC e a colagem FPC, são realizados testes de resistência ao descascamento para avaliar a durabilidade das colagens.
5. Envelhecimento após a montagem
Os módulos montados passam por um processo de envelhecimento com aplicação de energia para garantir confiabilidade a longo prazo.
6. Embalagem e Envio
Depois que os módulos passam por todos os testes e inspeções, eles são embalados e enviados ao cliente ou à próxima fase de produção.
